第635号 新人にバリデーション(妥当性確認)を伝えることは難しい
バリデーションの必要性がなかなか理解出来ない
> この時期、具体的には5月頃、新人研修が終わり、各部署に配置された新入社員との会話の中で、
「医薬品製造業において品質検査が重要なことはわかるのですが、バリデーション(妥当性確認)の必要性って正直ピントこないのです」と言った話をちらほら聞くことがあります。
■ 実は私自身も「バリデーション」について学び始めた時、例にもれず?医薬品こそ「人の命に係わる製造業だから、より厳しくバリデーション(妥当性確認)が必要になるのだろうな」くらいにしか思っていませんでしたが、「なるほど!これが理由の1つなんだ!」とちょっとガテンがいったことがありました。
⇒ そこで、今回は「なぜ医薬品製造業にはバリデーション(妥当性確認)が必要なの?」のごく一部の解釈ではありますが、製造方法とその試験・検査方法から考えてみたいと思います。なお、医薬品製造業に携わる方にとっては「なにをいまさら」とお思いかと存じますが、お付き合いいただけたら幸いです。
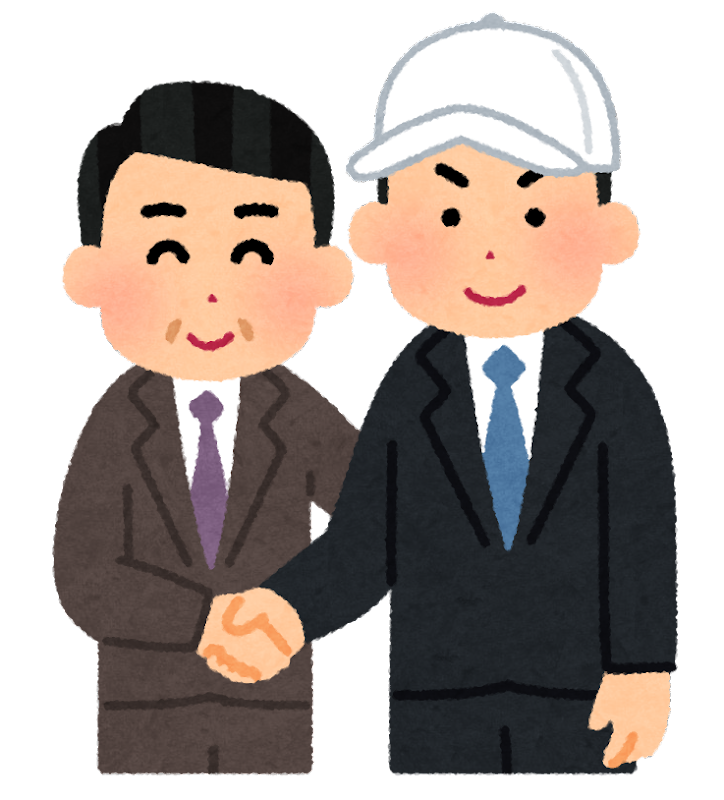
製造業の代表的な2つの製造方法とその試験・検査方法
> まず最初は、「製造業の代表的な2つの製造方法とその試験・検査方法」の違いを考えてみましょう。
製造業とは「原材料に加工を施して製品を生産する産業(デジタル大辞泉)」で、覚えきれないほど多くの業種がありますが、製造方法によって「プロセス製造」と「ディスクリート製造」として、大きく2つに分ける事ができます(中にはその両方を持ち合わせる会社もあります)。
■ プロセス製造
流体・ガス・粉体など形が一定でない材料を主に扱い、レシピと反応と合成を主体とする化学的で物理的な変化で製品を製造する方法です。
代表的な業種には「石油」「化学」「化学製品」「金属」「鉄鋼」「紙」「パルプ」「薬品」
「医薬品」「ガラス」「セメント」などがあります。
プロセス製造の主な試験・検査は「破壊試験・検査」となるため、基本的にはロット検査(抜取検査)となると思います。ゆえに、「未試験・検査品」を含めた1つ1つすべての製品の品質において保証することは困難です。
■ ディスクリート製造
部品を加工組立で製品を製造する方法です。
代表的な業種には「自動車」「電子機器(パソコン・家電)」「医療機器」などがあります。
ディスクリート製造の主な試験・検査は「非破壊試験・検査」となるため、必要に応じて「ロット検査(抜取検査)」や「全数試験・検査」などを選択することが可能です。
⇒ したがって、「医薬品」はプロセス製造でありながら、かつ、「人命や健康に直結した製品」となるため、本来は全数試験・検査の対象とすべきですが、「破壊試験・検査」を実施したら製品として供給できなくなってしまいます。
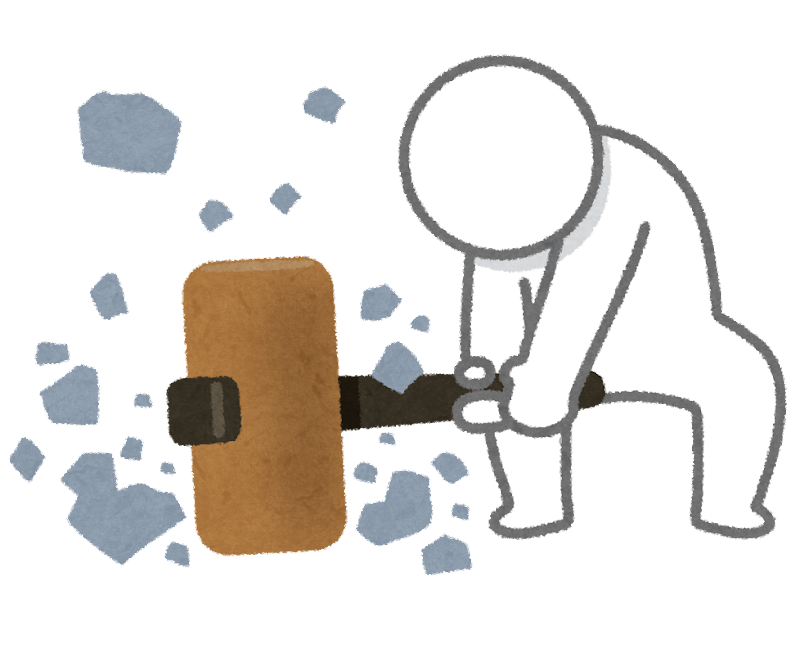
バリデーション(妥当性確認)の定義の難しさ
> では、どうすれば製品を破壊せずに、製品1つ1つの品質を保証できるのでしょうか?
全数試験・検査ができないのならば、プロセスの方に着目し、製造プロセスの開発・設計の段階から、より良い品質を継続的に作り込み、かつ、それを証明するための仕組みが必要になるかと思います。それが、「バリデーション(妥当性確認)」という科学的手法につながります。
たとえば、GMP省令ではバリデーションの定義とその進め方が次のように表記されています。
■ GMP省令でのバリデーションの定義
2. バリデーション指針
(1)バリデーションの目的等
バリデーションとは、製造所の構造設備並びに手順、工程その他の製造管理及び品質管理の方法(以下「製造手順等」という。)が期待される結果を与えることを検証し、これを文書とすることをいうものであること。
■ GMP省令でのバリデーションの進め方
2. バリデーション指針
(5)バリデーションの種類等
① 適格性評価(Qualification)
新たに据え付け又は変更する設備、装置又はシステムについて、個別に又は適宜組み合わせて適格性を評価し、文書とする。通常、以下のア.からエ.までの適格性評価を順次段階的に行っていくことが基本となる。イ.以降の適格性評価では、適切に校正を行った計測器を用いることが求められる。
② プロセスバリデーション(Process Validation:PV)
工業化研究の結果、既存の類似製品の製造実績等に基づく製品品質への影響要因(例えば、原料等の物性、操作条件等)を考慮して設定した許容条件の下で工程が稼働し、求められる品質の製品が恒常的に得られる妥当な工程である旨を検証し、文書とする。
⇒ しかし、プロセスに着目する必要性は理解できても、この規定だけで「バリデーションの仕組みや手法」を理解するのはなかなか難しいと感じます。
バリデーションの流れを図で確認してみよう
> そこで、当社なりにバリデーション(製造設備)を図式化したものが「第631号 バリデーションの流れと校正(キャリブレーション)の関係がパッと見てわかる !」です。
■ 「設備開発・設計」などかなり早い段階から始まり、「生産開始」の直前までの工程の中で実施していくため、これらのバリデーションの中のプロセスを1つ1つ継続的にひも解いて検証していく事が求められています。
⇒ とはいえ、「プロセス製造」と「ディスクリート製造」の違いを押さえることで、ひとまずは「バリデーション(妥当性確認)」の必要性を感じていただけるのではないでしょうか。
▼ 「バリデーション、校正(キャリブレーション)」についても「無料オンライン相談会」からご相談していただくこともできます。
※ 当社は、フィールドでバリデーション・キャリブレーションを実施する立場から、規格の要求内容や定義を具体化(具現化)して、お客様に満足して頂ける作業をお届けする努力を続けています。
最後まで、お読みいただき有難うございました。